Sécurité machine : démarche d'appréciation et de réduction des risques
Grâce à l'accompagnement conjoint de la Carsat Aquitaine et de l'INRS, l'entreprise LAUTIER, constructeur de machines "spéciales", a su intégrer la démarche d'appréciation et de réduction des risques lors de la conception pour fournir une machine sure et conforme.
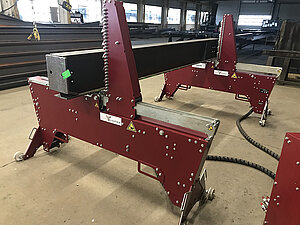
Démarche d'appréciation et de réduction des risques
L’objectif de la démarche proposée et de s’assurer que tous les risques soient bien identifiés et pris en compte puis de valider le choix des mesures de protection mises en œuvre, notamment concernant le dispositif de commande des mouvements du bras.
Il est à noter que pour répondre aux exigences de la Directive Machines 2006/42/CE, relative à la conception des machines, la démarche concerne tous les risques (pas uniquement mécanique, mais également électrique, rayonnement, bruit...) et ce à chaque étape du cycle de vie de la machine (transport, manutention, réglage, production, nettoyage...).
La normalisation européenne propose une démarche générale (norme NF EN ISO 12100).
Pour en savoir plus, consultez la brochure INRS "Evaluation des risques et conception de machines" (ED6389).
Déroulement de l'accompagnement pour mise en œuvre de la démarche
Réunions visios tripartites (Constructeur - INRS - CARSAT Aquitaine) :
- Exploitation des documents remis par le concepteur.
- Présentation de la méthodologie au concepteur avec transmission de la documentation utile (à consulter dans l'onglet "En savoir +" de la rubrique "Présentation").
- Réalisation d'une première étape d'appréciation globale par le concepteur suivant les recommandations et rédaction d'un dossier d'analyses de risques.
- Commentaires, corrections, précisions sur les éléments présentés, notamment portant sur la notice d'instructions.
- Révision de l'identification des phénomènes dangereux, de la méthode d'évaluation des risques (cotation) et des pistes de mesures de prévention à mettre en œuvre pour supprimer ou réduire les situations identifiées.
Un focus a ensuite été réalisé sur les risques d'origine mécanique en phase d'exploitation : écrasement, cisaillement, heurt, des membres supérieurs liés aux mouvements des bras mobiles de la machine et des barres manipulées.
Développement de l'argumentaire et justification du choix de la mise en place d'une commande à action maintenue par l'opérateur pour tous les mouvements de l'équipement :
- Protection de l'opérateur : positionnement du pupitre de commande en dehors de la zone d'évolution de la machine et des barres, nécessité d'action maintenu des 2 mains de l'opérateur sur des organes de commande prévus à cet effet pendant tout le cycle. Le relâchement d'un organe de commande provoque l'arrêt.
- Protection des tiers : visibilité parfaite de la zone d'évolution des mouvements de la machine et des barres. Vitesse "lente" des mouvements, contrôle permanent des mouvements par l'opérateur (pas de cycle automatique ou enchainement de mouvements).
De cette 1ère phase d’appréciation des risques, il ressort que la protection des personnes vis-à-vis des risques mécaniques (écrasement, cisaillement, heurt...) pouvait reposer sur la mise en place d’une commande "bimanuelle" à action maintenue pendant tout le cycle à condition que celle-ci assure la fonction de sécurité.
Restait donc à déterminer le niveau de risque attendu de la fonction de sécurité associée à la commande bimanuelle pour atteindre l'objectif visé de réduction des risques (en l'occurrence un niveau de performance PLc suivant la norme EN ISO 13849-1).
Pour en savoir plus, consultez la page "Les modifications".
Toute la démarche d'évaluation, les résultats des calculs et justification des choix sont formalisés dans un document spécifique "Analyse des risques" intégré au dossier technique.